【ネオジム磁石の製造工程・全体概要】
下図はネオジム磁石の製造工程です。今月はこの中の成形工程についてのお話をしましょう。成形工程はネオジム磁石製品の形状の原型を作るためや異方性化して磁石の一定方向の磁力を強くするための重要な工程になり、磁界中成形または磁場中成形などと呼ばれています。
1.磁場中成形の原理
先月号でお話しました粉砕工程後の材料粉を磁場成形機で圧縮成形します。(金型は非磁性体で磁場が通ります)この時、粉末材料の一粒一粒は成形機の磁場と同じ方向に、それぞれの磁化容易方向をそろえるように動き、整列し、圧縮されて固定されます。なお、磁場成形機には圧力伝達方式の違いにより油圧成形機、機械式成形機に分かれ、さらに磁場の印加の仕方により、直角磁場(横磁場)方式と平行磁場(縦磁場)方式があります。前者は圧縮方向と直角(垂直)の方向に、後者は平行な方向に磁場を加えながら成形するものです。(下図参照)
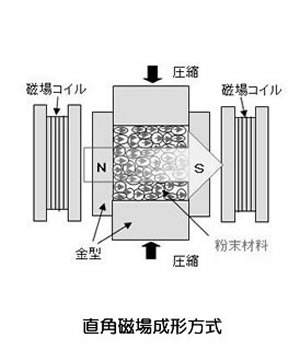
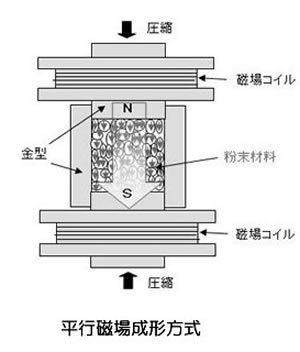
2.残留磁束密度Brを左右する配向度について
磁石の性能を左右する重要な特性項目のひとつに残留磁束密度Brがありますが、異方性磁石ではこのBrに影響を与える主な因子は次のようなものになります。
- 材料の飽和磁化Isの大きさ。
- 磁石中の結晶の磁化容易軸方向への整列の度合い(配向度)f。
- 焼結体の相対密度d(焼結密度/理想密度)。
この中で配向度fは成形の仕方によって大きく左右されます。
一般的には直角磁場方式の方が良好な配向度が得られ、平行磁場方式に比べ残留磁束密度Brで約10%向上しますが、リング型製品や円柱型、角型製品の薄物を最終製品に近い形状(ニアネットシェイプ)で成型する場合は平行磁場方式で成型せざるを得ません。
印加する磁場については、電磁石による直流磁場は金型内で1.5T以上必要と言われています。配向度は磁場強度が高いほど高くなりますが、実際の磁場印加方法は鉄心付き電磁石による静磁場または空心コイルとコンデンサバンクを用いたパルス磁場により行われます。後者は大振幅の磁場を印加でき、磁場印加方向を数回切り替えることにより配向度が向上するという現象が見出され、交番磁場配向法として50MGOe以上の高性能ネオジム磁石の成形に利用されています。さらに、電磁石による磁場配向において原料粉体を磁界強度の勾配のある空間に位置させることにより、成型金型のキャビテイ内でわずかに移動できるようにする勾配磁場配向(または傾斜磁場配向)という方法も開発され、これらの組み合わせ技術により焼結磁石の配向度は最高99%以上に達しています。
3.工業的な規模での成形機について
そして、ネオジム磁石は前記1、2で解説しました“異方性磁石”、“粉末冶金”の両者の長所を生かすための製法で製造されます。すでにお話しましたように、ネオジム磁石合金は、ネオジム(Nd)、ディスプロシウム(Dy)、鉄(Fe)、ホウ素(B)、コバルト(Co)、および微量の銅(Cu)、アルミニウム(Al)などの成分から構成されていて、溶解工程で合金塊(インゴット)にします。ところが、そのインゴットは次図のように多くの結晶粒(黒線で囲まれた部分)の集合です。
国内の大規模量産工程では総圧100t以上の大型油圧成形機を使用し、ニアネットシェイプの多数個取りをする場合が多いようです。材料は微粉砕後または潤滑剤混合後の窒素充填チャンバーをそのまま成形機ホッパーとして装着し、材料の酸化を防ぐため成形機全体は窒素ガス雰囲気に置かれ、材料の金型充填から成形、コア取り、焼結トレイへのコア積みなどは全てロボットが行うようになり、自動化が進んでいます。
なお、一部の低酸素湿式法では微粉砕後の粉末を低酸素の油性液体と混合してスラリー化することにより、空気との接触を絶つ湿式成形機を使用しています。
成形後の成形体は空気と接触することなく窒素雰囲気または真空中に保管されるか、速やかに次の焼結工程へ運搬されます。大規模量産工程では保管、運搬は全て窒素雰囲気中コンピュータ制御で自動的に行われます。
一方、中国ではニアネットシェイプでの成形はほとんど行われず、母材ブロックからの加工により製品形状にする工程がほとんどのようです。したがって、母材ブロックのような大型成形体の成形では、均一な成形密度が得られない場合があり、磁場成形の後にCIP(Cold Iso-static Pressing)などの静水圧成形を行うことにより、配向を低下させずに十分な成形密度と均一性を得ることができる工程を追加しています。中国での成形方式が母材ブロック中心になっている主な理由は、(1)成形機の剛性、部品精度の問題があり、精度の高い大型成形機が製造できない、(2)金型の材質、寸法精度、ヨーク組み込み技術等のレベルに問題がある、(3)加工機および加工コストが安い等になります。
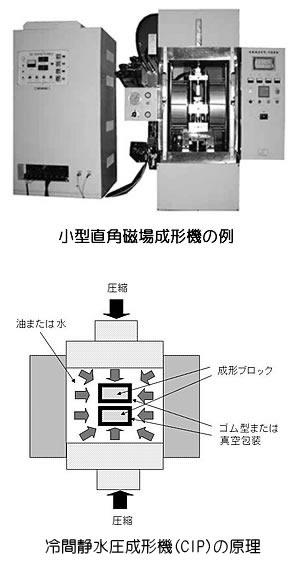
なお、高性能磁石を製造するために高い配向度を実現することは磁石製造に共通するテーマではありますが,ネオジム磁石ではさらに工夫した方法が考案されています。配向度は一般に磁場による整列と、プレス圧縮による整列の乱れとの競合で決まります。整列の阻害要因としては、粉粒子間,粉体とダイスの間の摩擦が考えられます。原理的にはなるべく高い磁場を用い、等方的に圧縮するのがよいことは明白ですが、これを工業的生産の場で行うのは容易ではありません。佐川らはパルス強磁場とラバープレスを組み合わせたRIP法(Rubber Isostatic Pressing、ラバー静水圧成形)を開発しました。
右図はその金型回りの概略を示しています。ダイ・プレスではありますが、金型中に挿入されたゴム型を介して、粉体は擬似静水圧を受けます。原料粉体をあらかじめ軽く圧縮した後、パルス強磁場を加えて配向させ、加圧成形します。通常の平行磁場プレスに比べ優れた配向度が得られるので一部高特性磁石の生産に採用されています。
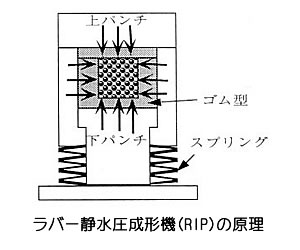
以上、今月は磁場中成形工程について解説しましたが、近年の50MGOeを越える超高性能ネオジム磁石の実現には、国内メーカーによるこの工程における高配向度追求、低酸素化などの製造技術的な進歩が大きく寄与しています。次回は焼結・熱処理工程のお話です。
(参考資料)
「永久磁石・材料科学と応用」佐川眞人・浜野正昭・平林 眞 (アグネ技術センター)
「希土類永久磁石」俵 好夫・大橋 健 (森北出版)
「NeoMag通信バックナンバー・2006年10月号」